Ferromatik Europe
|
|
The K-TEC Series
For Demanding High-Performance Applications
Exceptional precision and repeatability, fast cycle times, high injection rates and pressure, parallel functions, and easy maintenance: these are the hallmarks of the K-TEC Series of Injection Molding Machines.
High performance hydraulic and hybrid K-TEC machines keep molders in the lead by offering competitive manufacturing solutions for everything from the simplest to the most demanding applications, including multi-cavity molding, challenging material combinations and integrated process molding.
|
|
Clamping Unit
The clamping unit in the K-TEC series use a three platen assembly. Together with a FEA optimized sub-assembly and directly attached platen, this design guarantees the highest degree of precision with even the heaviest molds along with outstanding platen parallelism and low mould maintenance. The moving platen glides on a hardened rail assembly. The assembly is low friction and requires minimal maintenance.
Another plus is the large platen space for moulds with tie bar spacing (from 560 x 560 to 1000 x 1000 mm) and the support columns (hardened and surface finished) which are easily changed as required. Two separate traverse cylinders allow for easy opening and closing of the clamping unit. Pressure bolts connect the moveable plate with the clamping piston. This solves two problems with one solution: the clamping force is optimally positioned in the centre, and easy access to the ejector is ensured. The adjustable length of the pressure bolts grants variability in the mountable mould height.
Injection Unit
A solidly built linear bearing suport system ensures reliable operation. High shot volume and high injection pressure make these machines ideal for a
wide range of industry applications.
The whole injection unit assembly swivels out allowing easy access to the screw. The screw barrel can be replaced within minutes.
The inline injection units of the K-TEC 175 through 450 models with revolving injection pistons are ideal for the production of thin-walled parts at extremely high injection speeds.
A consistent modular design philosophy offers numerous advantages, for example in the inection unit configuration. Aside from standard- and mixing
screws, barrier screws are also available for high performance applications in special lengths up to 25:1 L/D. Electrical screw drives are becoming an increasngly popular option here as well.
Drives
The greater the performance and dynamic range requirements of a particular task, the more reason to use a high-volume hydraulic accumulator. The K-TEC's standard hydraulic accumulators allow for a wide range of parallel movements. This guarantees short cycle times, an important economical consideration. Accumulator loading pump and pressure intensifiers are available to facilitate even faster injection moulding.
Controls
The Windows-based IQT control system is user-friendly and offers an excellent overview of the system. User-defined pages allow the operator to search setpoint values in any order and place them on three separate screen pages. Saving background data sets shortens setup times. Mold changes are easily activated by the relevant background data set. Thus production is quickly and simply changed over to new parts.
The IQT control system is also optionally available as IQT.net. This system adds an interface for OPC (OLE for Process Control) and provides a means for Internet access. IQT.net opens up a whole new world of possibilities including online diagnostics, analysis of process and production data, and process visualization with standard software applications.
|
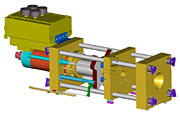
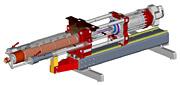
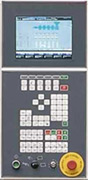
|
|